When it comes to maintaining roads and dikes in the Netherlands, one problem comes up again and again: the ground keeps sinking.
That’s not a metaphor. In regions built on soft soils like clay and peat, the weight of infrastructure slowly compresses the ground underneath. Over time, that leads to cracks, uneven roads, and costly maintenance. The usual fix is to add more material to repair the damages, but this can actually make things worse by increasing the pressure on already fragile soils.
That’s the challenge being tackled in Pilot #3 of the CIRCUIT project, based in South Holland. Rather than using conventional construction methods, this pilot is exploring an approach that’s both more sustainable and more efficient: using recycled industrial by-products to stabilise the soil.
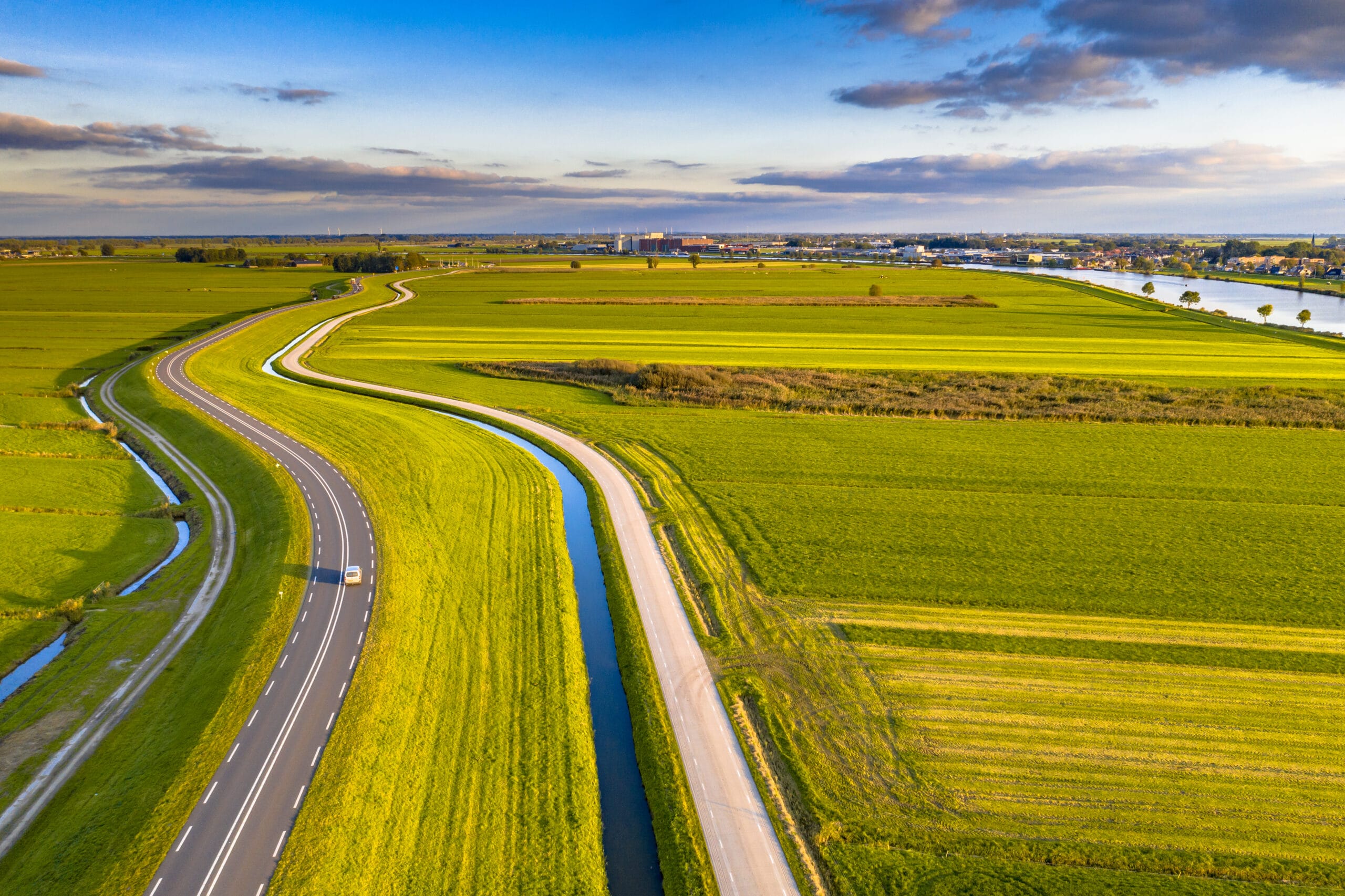
Aerial view of Coastal region with dike of IJsselmeer near Zwarte Water, Zwartsluis, Overijssel Province, the Netherlands. Landscape scene in nature of Europe.
The Pilot Site: Oostmolendijk
The pilot is taking place in Oostmolendijk, on a dike road between Ridderkerk and Hendrik-Ido-Ambacht, right along the river Noord. This section is part of Dike Ring 17 (IJsselmonde), a critical component of the regional flood defense network.
The site was chosen because of its history: in 2013, a reinforcement project on a nearby dike segment triggered a shear failure, essentially a structural collapse in the soil. As a consequence, the road was damaged, and it became clear that the standard approach wasn’t working in areas with unstable peat layers.
The Concept: Turning Waste into Reinforcement
The core idea is simple: instead of building heavier, build smarter by improving the soil itself. The pilot aims to stabilise the ground using secondary raw materials from industrial waste, such as:
- Fly ash: a fine grey powder produced when coal is burned in power plants, rich in silica and alumina, often used in concrete production for its binding properties.
- Blast furnace slag: a granular material left over from the steel-making process, formed when molten slag is rapidly cooled. It can be ground and reused in construction, where it helps improve durability and resistance.
- Geopolymers: a type of eco-friendly synthetic materials made by activating industrial by-products (like fly ash or slag) with alkaline solutions. They can form a solid binder similar to cement, but with a much lower carbon footprint.
- Other suitable industrial residues: depending on availability, these may include by-products from mining, energy production, or waste treatment processes that have potential for soil reinforcement.
These by-products are typically considered waste, which makes them more affordable than raw materials. But using them isn’t just cost-effective, it’s also better for the environment. Instead of being discarded in landfills, they’re given a second life in infrastructure projects, reducing waste and lowering the need for virgin resources like gravel or cement. This fits into a broader circular economy approach: keeping materials in use for as long as possible, cutting emissions, and making infrastructure more sustainable from the ground up.
These materials are currently being tested for their ability to improve the stiffness and load-bearing capacity of soft soils. The goal is to make roads and dikes more stable over time, while significantly reducing environmental impact compared to traditional methods.
This work is led by Waterschap Hollandse Delta (WSHD), with support from INGEO, the University of Zagreb, and Infraplan Consulting.
What’s Been Done So Far
Several key activities have already taken place since the beginning of the project:
1. On Site Investigations
In May 2024, the CIRCUIT Team carried out a range of measurements to understand the soil properties at the pilot site.
WHSD used two main methods for geotechnical tests: cone penetration, where a metal cone is slowly pushed into the soil to see how much resistance it meets, and borehole drilling, which involves drilling into the ground to collect actual soil samples.
Meanwhile, the University of Zagreb conducted geophysical tests using special tools to look underground without digging. One method, called electrical resistivity tomography, sends small electrical currents into the soil to detect what kind of materials are down there, wet or dry, soft or firm. Another method, MASW (Multi-channel Analysis of Surface Waves), sends sound waves into the ground and measures how fast they bounce back, which gives clues about how solid each layer of soil is.
Together, these non-invasive methods helped map out the ground layers under the road across three 100-metre profiles, establishing a baseline for future improvements. This information is important for choosing the best way to stabilise the ground.
2. Standards and Solutions Review
INGEO looked closely at the official rules and guidelines used in the Netherlands for soil stabilization, including the POVM framework which is a set of standards used by engineers in the country. They also created a reference database listing both traditional techniques (like adding sand or gravel) and newer, more innovative methods (like using recycled materials). By comparing all these options, the team can identify which methods are most promising, not just in theory, but also in practice.
3. Performance Metrics
Infraplan Consulting created a set of tools called Key Performance Indicators (KPIs). These are clear, measurable criteria that help the team judge how well each soil stabilisation method works. The KPIs look at things like safety, impact on the environment, and how well the solution holds up over time (long-term resilience).
The team is also putting together a technical report that explains each technique in more detail, how it works, where it’s already been tested or used, and what can be learned from those experiences to help improve other projects across Europe.
Reaching Wider Audiences
In April, WSHD organised an Open Day where they presented the pilot to local community and stakeholders. The event combined scientific presentations with more creative outreach tools including a comic strip that explains the problem of soil settlement and the role of recycled materials in stabilising the ground.
What’s Next?
In the coming months, the best-performing materials will be selected for a field demonstration at Oostmolendijk. The site will become a live testbed to evaluate how the selected recycled materials perform under real-world conditions.
In parallel, numerical models will simulate the long-term behaviour of the stabilised soil, looking at safety, durability, and how well the solution prevents further subsidence.
This Dutch pilot is part of CIRCUIT’s wider effort to support circular, low-carbon infrastructure. It shows that recycled materials aren’t just a waste solution: they’re a structural one too.